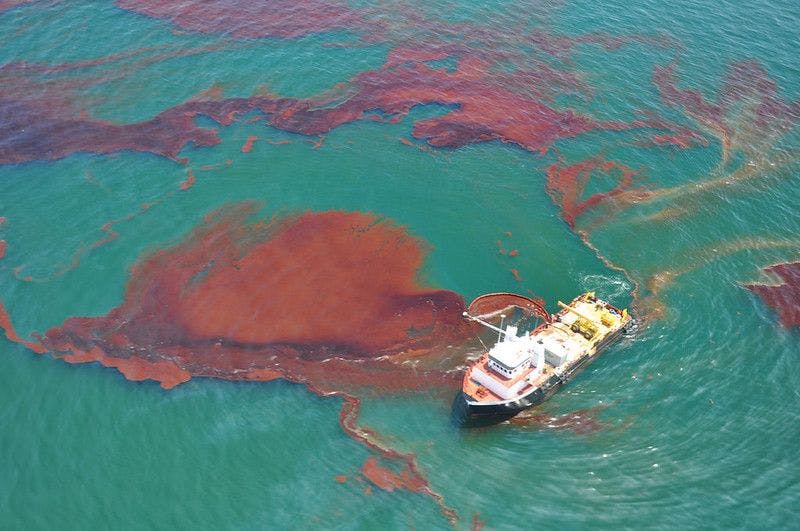
Managing economic crisis: Digital transformation is critical for facility management teams
On April 20th, 2010, a series of missteps caused a methane explosion that sank BP’s Deepwater Horizon rig, leaving 11 dead, 17 injured, and 4.9 million barrels of oil pouring into the Gulf of Mexico over 90 days. The impact to the environment and marine life was beyond devastating. Even now, a decade later, both the Gulf and BP continue to suffer the consequences. Endangered fish, turtles, dolphins, and other marine life in the region still experience reproduction failure, lung disease, and heart issues. Humans involved in the cleanup process are also encountering similar long term health problems. And BP? Well, as of 2018, its cleanup costs and legal fees ballooned to $65 billion.
Yes, that’s “billion” with a “B”.
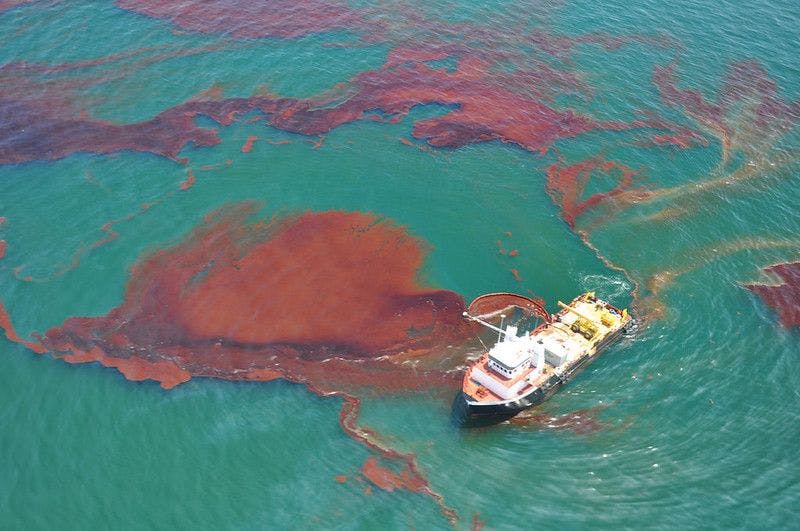
Skimming oil from Deepwater Horizon (Source: Flickr)
Digital transformation isn’t just about implementing the latest technology. It’s about changing the way we work and interact, supported by technological innovation. This new digital era requires teams to make a significant shift in business processes, culture, and customer experience in order to remain competitive.
For instance, jobs that typically require predictions or tedious manual effort, such as searching through engineering drawings for spare parts information, should become machine-based. Algorithms can plow through large volumes of data much faster than a human can. It’s better for us too, because it enables us to shift towards more complex decision-making—and humans are much better at that than machines.Making this shift can be tricky, especially when you’re also trying to wrap your head around current global events and adapt to the changes the pandemic has brought about. Fortunately, digital transformation actually addresses many of the issues businesses face today. In this article, we lay out some fundamental steps that your facility management team can take towards successful digital transformation.
Transforming your facility management team
There are two overarching principles to keep in mind as you build your digital transformation strategy: connect employees and integrate technological systems.
Enabling employee connectivity
In too many organizations, departments and data are siloed. It’s a major inefficiency and source of frustration for employees, whose expectations are driven by what they experience in their personal lives through the Internet and social media. Information is quick and easy to access. It’s especially the case with millennials entering the workforce: Digital is in their DNA. Facility management teams that shift towards this mindset and enable easy collaboration, information access, and remote work will empower employees and allow the team to thrive.
Some key steps you can take to facilitate employee connectivity include:
- Move data, such as digitized engineering drawings and other related documents into a centralized database that can be accessed remotely. This is imperative because if a team member discovers a piece of equipment is about to fail, they’ll need to quickly search the equipment number, find the related P&IDs, and figure out which part they’ll need to replace. Then, they should be able to do a stock check for spare parts, or place a purchase order if necessary. By improving data accessibility, maintenance processes become far more efficient, mitigating the risk of plant shutdowns or failures.
- Enable tablet or smartphone access to your systems for real time updates. This allows you to make the above process even more seamless as a maintenance worker could make all the necessary requests and changes on the spot. It’s especially useful if you struggle to get employees to fill out detailed maintenance work orders. They can quickly jot down all the information, snap a few photos of the issue, and ship to the next appropriate person. No more “I’ll get to that later”—reducing the risk of someone forgetting to file a report on an initially small issue that could potentially evolve into a much larger one due to neglect.
- Migrate from waterfall-based project management to Agile methodology. The economic and social situation we face today is highly uncertain. On top of that, maintenance and operations for facilities also have a high degree of unpredictability, especially when it comes to planning. Agile is very well suited for such environments. It facilitates responsive planning, continuous improvement, and self-motivation by allowing individuals to take greater ownership of their tasks and decisions. Moving your team into this adaptive planning methodology will allow you to quickly adjust to any sudden challenges, unlike a waterfall approach, which risks a project running much longer than it should. It’s not designed to detect errors early on, so folks tend to get trapped by a lot of vested time and interest, straying too long down the wrong path.
- Include other departments in planning meetings so they get a better understanding of your processes and challenges. It’s time to break down those siloes. Miscommunication, misunderstandings, and differing objectives often get in the way of getting things done. By keeping other departments aligned with your objectives, you are less likely to have projects you desperately need to kick off instead get stuck in procurement, for example, because they don’t realise the importance of what you’re trying to achieve.
- Implement other infrastructure for remote work, such as Slack for asynchronous communication and Clubhouse for task management. This has become particularly urgent as we find ourselves quarantined at home. There’s no reason for work to stop simply because you’re not in the office. If half the team is working onsite and the other half is at home, direct the latter towards maintenance planning and digitization tasks. Use these unprecedented times as an opportunity to achieve other important digital transformation objectives.
Integrating systems through Industry 4.0
Now we come to the other buzzword you’ve been hearing about: Industry 4.0. Just as your employees need to be better connected to each other through technology, you also need to make sure your various technological systems are communicating effectively amongst themselves and your team.
Tech talks to tech: The Industrial Internet of Things (IIoT)
One well-known IIoT initiative is to place sensors on critical equipment to collect data for predictive maintenance.
But that’s just the tip of the iceberg, and not even the first thing you should do because you won’t capture the ROI from that until you’ve taken fundamental steps, like gathering context from engineering drawings and other documents. You might also consider using drones to access hard-to-reach or unsafe areas to assess equipment and monitor surroundings. For example, drones can send photographs of cracks in buildings and pipelines for machine learning algorithms to analyze. The combined technology could also regularly capture and evaluate overhead imagery of the whole facility and its surrounding environment—Petroecuador might have been able to use that to predict and prepare for the landslide. Or, if a natural disaster has already occurred, computer vision algorithms can deal with the aftermath by assessing structural damage to help your team decide on safety measures and the personnel required for an appropriate response.
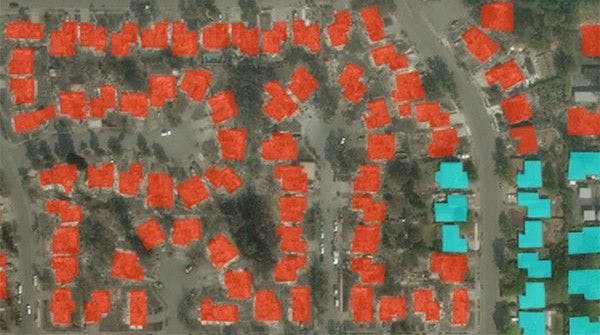
Computer vision algorithms can assess building damage levels in overhead imagery (Source: xView2)
Tech interacts with humans: Systems of Intelligence
Beyond just implementing Industrial Internet of Things (IIoT) systems, where tech communicates with tech, you also need a way for your team to integrate with the tech. Machine learning is typically a black box. Even with the latest trends in Explainable AI, when the models are incorporated into complex workflows where multiple algorithms feed into one another, it becomes extremely difficult to put reliable and meaningful model metrics into place.
Additionally, while machine learning can get you say, 95% accuracy for a particular task in record time, high-impact decisions relying on this data may require you to push the results to 100% accuracy. A good example of this is automated information extraction from P&IDs and other documents for equipment maintenance specifications. The data you collect here sets the foundation for countless critical decisions, so a human is required to remediate any errors that exist following the machine learning phase.
Systems of Intelligence are designed to rise to these challenges through human-in-the-loop machine learning. This means that for a given workflow, all machine learning and human quality control steps seamlessly flow within a single user interface. There’s no need to dig into code or rely on black box predictions, giving your subject matter experts (SMEs) more control over the process. Some examples of workflows in a Facility Maintenance system of intelligence may include:
- Digitizing and gathering context from engineering drawings, maintenance reports, etc.
- Combining sensor inputs with contextual information for root cause analysis
- Analyzing drone photographs to alert staff to potential issues and suggest corrections
Through a system of intelligence, your team can rely on Artificial Intelligence (AI) to handle the tedious effort of extracting and analyzing all of your large, variable, and unstructured data. Once the analysis is complete, it’s up to your SMEs to come into the loop and assess those predictions, then make decisions based on the results.
The timeline for transformation
Our ways of working are no longer in the process of changing. They have changed. For better or for worse, Covid-19 has crunched the timeline to now. To stay afloat and mitigate risk of disaster, facility management teams need to embrace and empower themselves with a digital mindset. From adopting agile project management techniques to combining the power of machine prediction with human decision making through systems of intelligence, these initiatives will arm you and your team to overcome the challenges of the next 18 or so months.
Recommended Posts
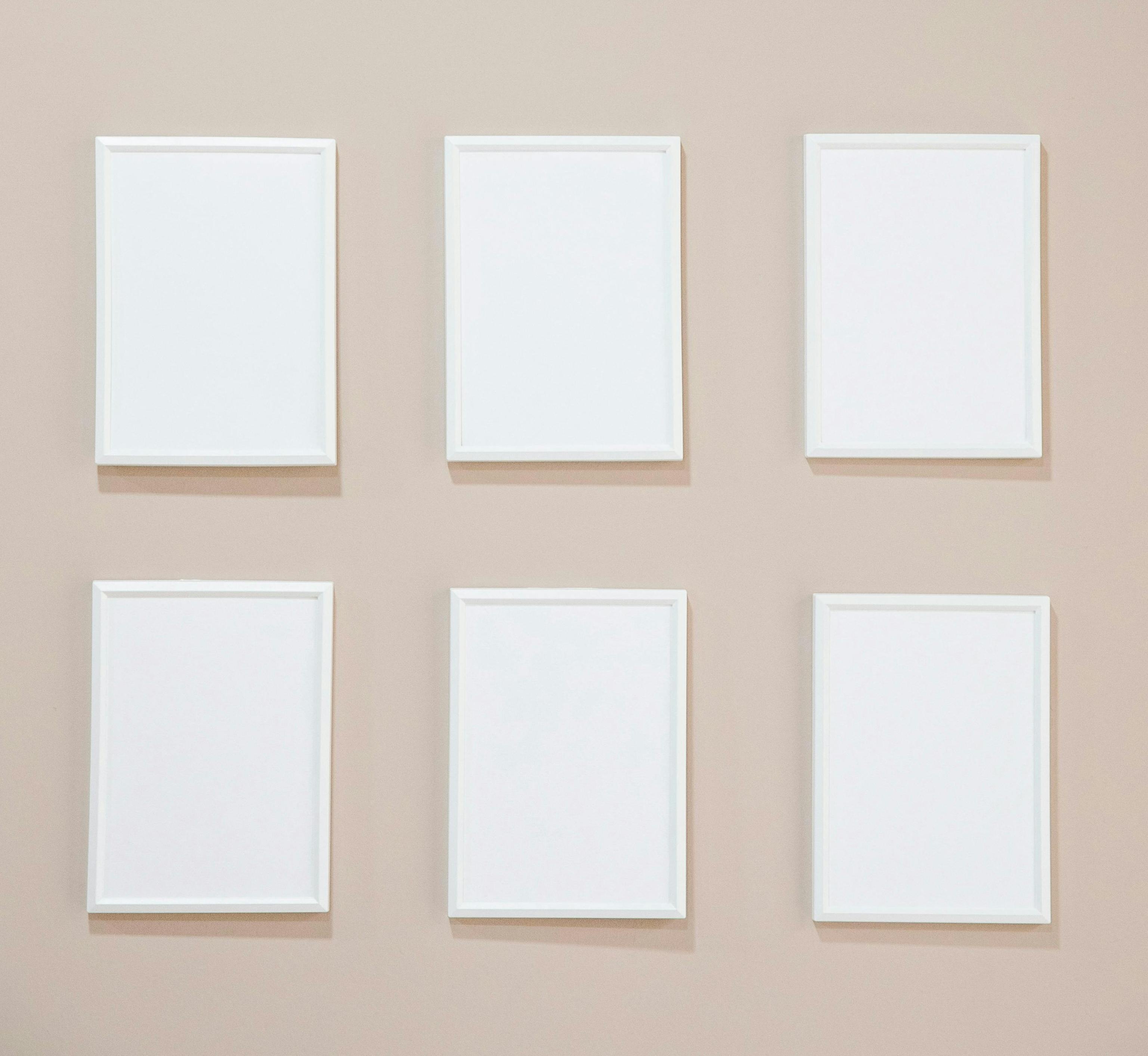
8/15/2024
A new era of enterprise search for facilities
(Part II): Data preparation
Before implementing new search technology, data cleanup and preparation is critical. Here's what you need to do.
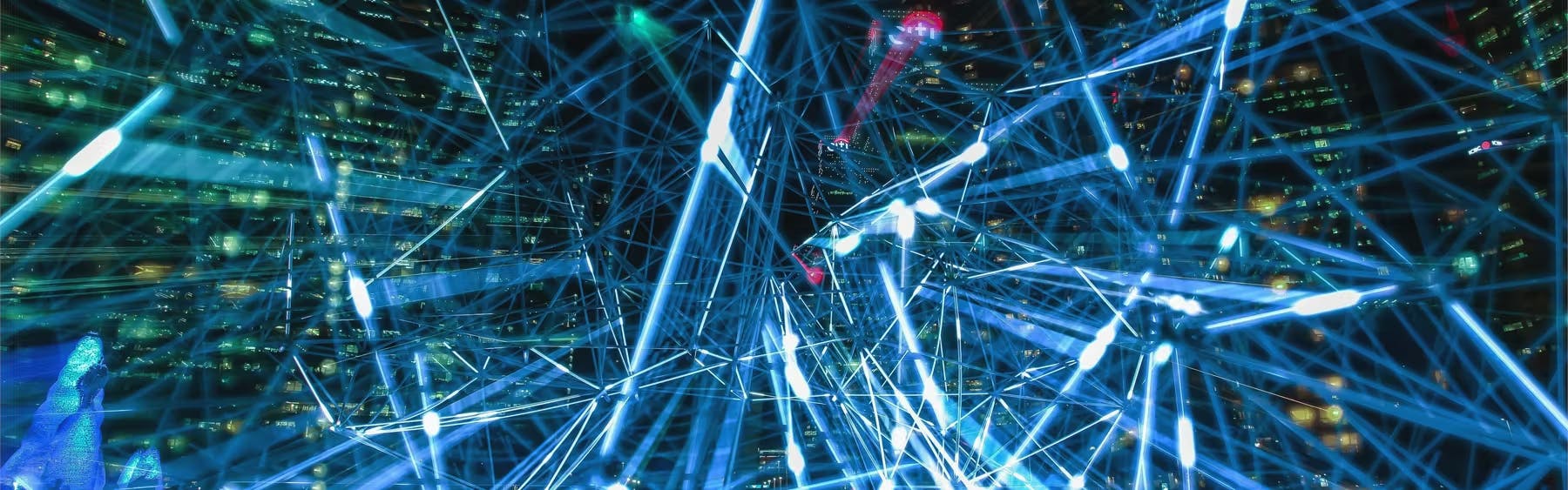
8/1/2024
A new era of enterprise search for facilities
Enterprise search is changing for facility operators—out with the file hierarchies and in with the information networks.
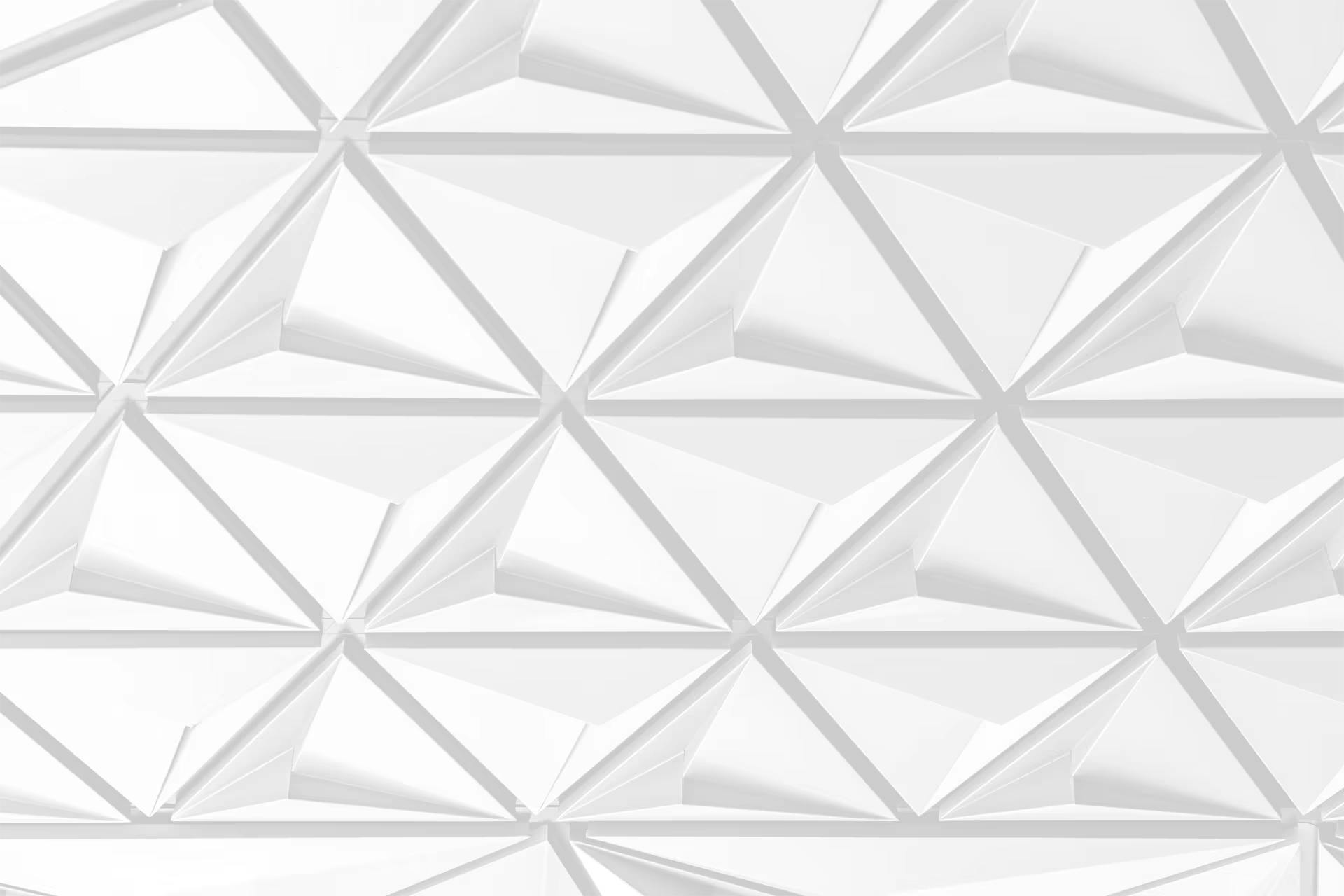
12/16/2022
Industry 4.0: The Unstructured Data Perspective
How to build a contextual platform that will be the launching pad for every one of your Industry 4.0 initiatives.